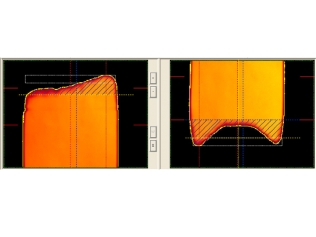
CropVision CV3000_Crop Shear Vision System for hot strip mills _DELTA
Xuất sứ: France
Nhà cung cấp: PTC
Hãng sản xuất: DELTA
CV3000, Delta Sensor Vietnam, Deltasensor Vietnam, Delta chính hang, Delta chinh hang, phân phối Delta Vietnam
- High Resolution Area Camera
- High Speed Capture of Head and Tail Profile
- Flexible & Multi Strategies Optimization
- Ethernet – Client Server Architecture
Hot Strip or Plate Mill - Background
The crop shear practice is very important for the Hot Strip Millsto avoid cobbles and steering problems in the finishing stands. Steckel Rolling operation for all coiled plate product also has problems if the front end is not cropped squarely, there are often problems with steering and cobbles which cause significant delays and loss of production. DELTA is offering a very cost-effective Vision System, for installation at the delivery side of the roughing mill, which can be integrated into the existing Crop Shear Control System. This is a well-proven system with many installations in various hot strip mills. This Vision System captures and optimizes the target cut line for each individual head and tail crop in real time. This technology offers as much as 0.2% of yield savings in most of high production hot strip mills through a simple implementation of such a system. The system will capture the images of each head and tail and overlays the optimized cut line based on shape & width and feeds that information to customer's shear control system. The following technical description explains how the system optimizes the cut line. |
![]() |
![]() |
![]() |
The overall results of the crop optimization system depend on accuracy of the different phase in this process :
- Determination of the optimal cut line.
- Detection before the shear and tracking accuracy of the bar.
- Control of the shear.
DELTA has extensive experiences working with customers to implement strategies, which protect the quality of the product while minimizing the amount of crop loss.
For the detection and tracking of the bar before crop shear, DELTA can offer a complete range of sensors, including:
- Scanning hot metal detectors Rota-Sonde DC,
- Fibre hot metal detectors for detection below roll table: IRIS
- Velocimeter Velas DL4000 to measure speed,
- Heavy duty pulse generators GDP and GDC.
Description
A high resolution area CCD camera is mounted in a water cooled rugged enclosure at the exit of the last rougher. This camera feeds video frames to the Vision System computer captured in a fraction (1/1000) of one second to eliminate any impact of blurring due to speed of the bar. The computer searches each frame for a significant transition in video light levels : a dark to bright transition indicates the presence of the head end of the bar; a bright to dark transition indicates the presence of a tail end.
High speed pattern recognition software then intelligently analyses the image and precisely determines the complete profile of the head and tail end.
An optimal cut line is determined in accordance with the unique shape of the head and strategies that are applicable for the particular gauge, grade and customer specifications. The captured image of the bar together with the cut line, is displayed for the operator. The operator has time and controls to adjust the cut-line if there are special circumstances which require manual over-ride.
Similarly, the image of the tail of the bar is captured, analyzed, and an optimal cut point is determined.
As the transfer bar approaches the crop shear, the CropVision CV3000 transmits to the crop shear controller, the optimal cut length information, operator's over-ride along with any other pertinent information. In this way the crop aim point is independently set for each end of the transfer bar according to the unique shape of the bar plus any operator bias.
The CropVision CV3000 supports Ethernet TCP/IP and RS232/RS422 communications to the host computer and to the shear controller. A Profibus-DP option is also available.
Main screen
The screen shows the head of a bar, with the cut line and the following information: cut or skip decision, cut length, bar id, bar width at the base of the head, cut weight, and offset. The tail is shown in a similar manner on the screen. A bar end (head or tail) is shown from the time it passes under the camera until the time it is cut. If there are two heads between the camera and the shear the leading head will be displayed. Tails are similar.
The lower part of the display tracks the progression of bars as they move from the camera to the shear. The status of all alarms is shown to the top right of the panel.
The system allows configuration of the different parameters through menus which are password protected.
Transfer Bar Shape Determination
The edge detection algorithm enables the system to find a starting point on the leading edge of the bar. The system looks for the maximum light level gradient along a vertical line within the captured image. This point is the end of the bar. From the starting point determined above, the system follows the contour of the bar by tracing the gradient profile through the image.
Cut Line Determination
Once the shape of the bar has been determined, the system calculates the location of the optimal cut line in accordance with four criteria : a percentage of full width criterion, a fishtail criterion, a minimum cut criterion, and a maximum cut criterion.
- Percent-Cut Criterion
The percent-Cut criterion states a width percentage tolerance that the end of the bar must fulfill after it has been cut. For example, if the base width is calculated to be 2000 mm, and the Percent-Cut criterion is 90%, the cut line will be located at the point where the bar is 1800 mm wide, if this constraint is binding.
- Fishtail Criterion
If a bar is determined to have fishtail, the fishtail criterion specifies how much solid material must connect the two "ears" of the fishtail crop. For example, if the fishtail constraint is set at 50 mm, the crop cut will have at least 50 mm of solid material between the ears.
- Minimum Cut Criterion
If there is no fishtail on the end of the bar, the minimum cut criterion will determine the minimum crop cut to be taken. This constraint overrides the percent-cut criterion, so that the system will never call for a crop cut less than the minimum cut value.
- Maximum Cut Criterion
The maximum cut criterion determines the maximum crop cut to be taken. This constraint overrides the percent-cut criterion, so that the system will never call for a crop cut longer than the maximum cut value.
Crop Cutting Strategies for Optimization
Once the image has been captured and analyzed, the CropVision CV3000 determines the optimal cut point. Two factors are considered when determining the optimum length of the crop: the shape of the end of the transfer bar, and the 'cut strategy'.
A 'cut strategy' is a set of rules that are applied to the shape of the bar to determine the optimal cut point. The appropriate strategy for any given transfer bar end may depend upon the steel chemistry, the final gauge, the end customer or other factors. For example, coils to be sold as hot rolled bands may require a different cropping strategy from those to be sold as cold rolled sheet.
The DELTA Crop Shear Optimization System is the most flexible system available, having the capability to store up to twelve (12) independent cut strategies. The appropriate strategy for each bar is downloaded from the host computer as part of the set up message.
Manual operation
The shear operator can easily over-ride the cut line determined by the CropVision CV3000 and adjust the cut line position manually with 2 scroll bars.
Main features
- High resolution area camera capturing in a fraction of a second the complete image of the Head / Tail. Insensitive to change in the speed of the bar.
- Advanced edge detection software and data capture processor.
- High speed CPU executing digital filtering algorithms for edge locations and transfer bar - plate shape determination.
- Most flexible system available with selectable cut strategies.
- Modular architecture allowing easy extension and implementation of effective solutions with end users.
- User friendly high resolution graphic display.
- Client Server architecture with multiple displays on a network.
- Design for the steel industry harsh environment.
- Simplicity of installation and maintenance.
- Remote dial up Access Service through network for trouble shooting.