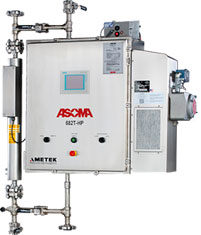
682T-HP Sulfur Analyzer- Máy phân tích lưu huỳnh 682T-HP
Nhà cung cấp: Pitesco Việt Nam
Hãng sản xuất: Ametek

The ASOMA 682T-HP is designed for the on-line analysis of sulfur in highly viscous hydrocarbons such as crude and residual oil using XRT (X-ray Transmission) technology. This system is ideal for high temperature and pressure sample streams. With its rugged, time-proven proportional counter detector and X-ray tube source, the 682T-HP gives superb analytical precision with a sulfur limit of detection of 200 ppm. The 682T-HP key features include a fully integrated densitometer, automatic density compensation, touch-screen controls, password protected and rapid update rates.
Overview- Ideal for analysis of crude and other highly viscous hydrocarbons, pipelines, terminals, blending
- Sample stream temperatures in excess of 662˚F (350˚C)
- Proprietary window in flowcell can withstand pressures up to 800psig/55 bar (consult factory for higher pressures)
- Certified to industry standards
- Large flowcell diameter (2 inches/5 cm) reduces interferences
- Analysis range for sulfur of 0.02-6.0%
Operation of the analyzer is regulated by an integral processor. The processor monitors instrument parameters such as process temperature, density, and system diagnostics. It also provides a comprehensive suite of alarms and a standard platform for communicating to a plant-wide DCS. Due to its unique design and robust construction, the system has minimal, if any, sample conditioning and recovery requirements.
ASOMA Instruments was established in Austin, Texas, in 1979 as one of the first companies to offer low-cost benchtop ED-XRF instrumentation. Since then, the ASOMA brand has become an industry leader with the development and release of the Models 100, 200 and 200T-series, and Titan line of XRF analyzers, as well as instrumentation for measuring sulfur in hydrocarbon streams
Specifications-
Process Conditions | |
Normal Product | Crude oil, heavy hydrocarbons, bunker fuels |
Sulfur Concentration | 0.02 - 6% |
Pressure at flowcell | Up to 800 psi * |
Flow rate at cell | Up to 200 liters/ minute |
Temperature | 662ºF/350ºC * |
Density Gauge | Required (supplied by AMETEK or the customer) |
Ambient Temperatures | Minimum 15ºC, maximum 40ºC * |
* Contact an AMETEK Representative for Special Requirements | |
Enclosures | |
Standard | Stainless steel, NEMA 4X (IP-65), NEMA 7 Ex d |
Dimensions | Controller 36x30x12 inch minimum |
Purge | Type X for Class I, Division I, Groups A - D area classification, (ATEX Category 2) or Type Z for Class I, Division 2. Groups A - D area classification, (ATEX Category 3) |
Optional | Heating and Air Conditioning System |
Power | 115 or 230 VAC ± 10%, 50x60 Hertz, 80 W typical, 300 W max |
Controller | |
Interface | |
Class 1 DIV 2 | External Touch Screen Interface, Power Switch, Valve Control Switch, Remote/ Local Control Switch, Capture Enable |
Class 1 DIV 1 | Internal Touch Screen Interface, Power Switch, Valve Control Switch, Auto Start/Stop Switch, Capture Enable |
Standard Outputs | 4-20 mA for sulfur and density, dry contact for common alarm, enclosure safety alarm, data valid, in bounds signal, RS-485 serial data |
Optional Outputs | Profibus, Modbus, Ethernet |
Standard Inputs | Densitometer input, dry contact for analyzer stop/start, mode switching |
Measurement Flowcell | |
Technique | X-ray Transmission (XRT) |
Analysis Time | Nominally 100 seconds |
Typical One Sigma Precision | ±50 ppm @ 0.1 Wt% sulfur ± 30 ppm @ 3.2 Wt% sulfur (consult AMETEK for application) |
X-ray Source | X-ray tube |
X-ray Detector | High resolution gas filled proportional counter Leak Detection: Capacitive leak sensor |